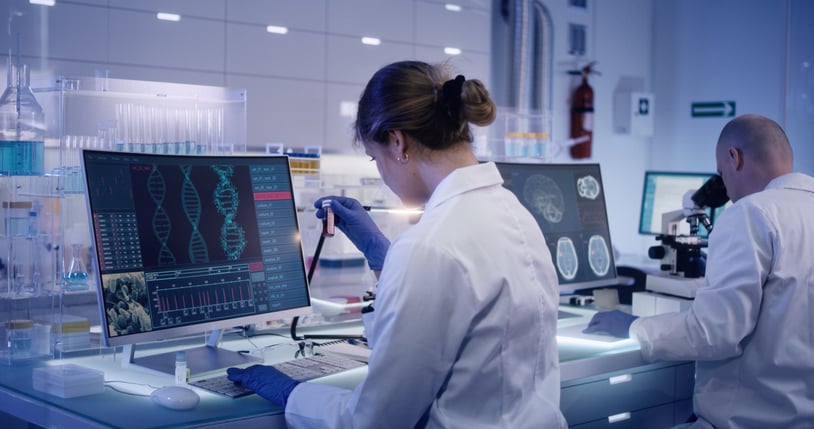
Healthcare & Medical PCB Applications
Hi-Tech Research. Precision Microscope Services. Air Monitoring Equipment. Smart Home Healthcare. Life-Sustaining & Life Saving Devices.
Considerations for Healthcare and Medical Device Contract Manufacturing
Class 3 medical devices, regulated by the ISO 13485 standard, require rigorous quality control and meticulous design, particularly for electronic enclosures that ensure biocompatibility, sterilization, and heat dissipation. Partnering with an expert electronics contract manufacturer is key.
Enclosure Design:
Class 3 medical devices and the ISO 13485 standard are crucial components in the medical PCB assembly industry, ensuring the safety and quality of PCB healthcare products. Class 3 medical devices are considered high-risk devices, as they are often implanted or used to sustain life. Examples include pacemakers, implantable defibrillators, and certain types of prosthetic heart valves.
The ISO 13485 standard for electronics manufacturing is an internationally recognized quality management system specifically designed for the medical device industry. It provides a framework for organizations involved in medical devices:
- Design
- Development
- Production
- Installation
- Servicing
Medical PCB manufacturers play a vital role in producing high-quality, reliable, and safe electronic components for Class 3 medical devices. Manufacturers must adhere to stringent quality control measures and follow established manufacturing processes to ensure the PCBs meet the necessary standards for medical applications. This includes using high-quality materials, implementing rigorous testing procedures, and maintaining detailed documentation and traceability throughout the manufacturing process.
Whether they're referred to as box-builds or integrated systems, electronic enclosures combine:
- Circuit boards
- Routing cables and wires
- Subassemblies
- Enclosures
In shorter terms, electronic enclosures are the finished and operable product.
Medical device electronic enclosure design must consider biocompatibility, sterilization methods, and ease of assembly and maintenance. Materials used in the enclosure must be carefully selected to ensure they do not interact negatively with the device or the patient. Additionally, the enclosure design must facilitate proper heat dissipation and allow for necessary connections and interfaces.
Manufacturers of Class 3 medical devices and those seeking ISO 13485 certification must work closely with medical PCB manufacturers and enclosure design experts to ensure their products meet the highest standards of quality, safety, and regulatory compliance.
To ensure the success and longevity of your enclosure, keep these design tips in mind:
- Get the right fit. You don't want your components bouncing around and potentially becoming damaged during operation
- Choose the best materials for the components' needs. If you need your components to be waterproof or shockproof, choosing wood would not be a suitable option
- Ensure adequate transmission
- Select thoughtful layouts and designs. The more intricate your design, the harder it will be to fix
- Check for compatibly with all of the components in the system
IPC Class 2 Electronics:
Class 2 IPC electronics are expected to work in industrial environments that require continuous performance. Unlike Class 3 IPC electronics, the safety of the operators are not at stake with Class 2. Examples of Class 2 electronics include microwaves, air conditioners, and televisions.
When your design can use class 2 electronics, remember these characteristics:
- Class 2 electronics can have up to 50% of their components "off the pad"
- Class 2 electronics use around 90% of the same components as Class 3, but have less-strict manufacturing standards and processes
- Documentation and testing for class 2 electronics are less stringent than for Class 3
Designing PCBs With LED Indicators:
Designing an LED PCB means designing for heat transfer. Since many components and instrumentations use LED lights as on/off, status, and warning indicators, significant amounts of heat can be produced, which can damage the board over extended periods of use.
To manage heat on your LED integrated PCB:
- Install/design proper heat sinks
- Use heat pipes and vapor channels
- Choose a metallic-core design for your PCB.
Want to Learn More About Medical PCB Manufacturers?
Download Our One-Sheet
Matric has won awards for maintaining on-time delivery. The award qualifications include:
- A level of quality of less than 3,000 DPM
or 99.7% - On-time delivery of 95% or better
- A minimum sales total
Want more information about how a full-service contract manufacturer can augment the abilities of your company and your equipment in the medical industry?
Fill out the form to download our one-sheet and see what Matric can do for you!